配件周转率
以下是关于配件周转率的专业分析,分为五个部分进行阐述:
一、配件周转率的核心价值
配件周转率是衡量企业库存效率的核心指标,计算公式为:年度销售成本 ÷ 平均库存价值。该指标量化了库存配件在会计周期内的流通次数,直接反映企业将库存转化为现金的能力。在制造业领域,行业领先企业的周转率通常维持在8-12次/年,而汽车后市场优质服务商的周转率可达15-20次/年,显著高于行业平均的5-7次。
二、动态平衡的艺术
1. 高周转优势:某工程机械代理商通过实施JIT模式,将周转率从4.5次提升至9.2次,释放流动资金3800万元,仓储成本下降42%
2. 风险临界点:当周转率超过供应链响应速度时,某电子企业遭遇芯片短缺导致产线停工,单日损失超200万元
3. 平衡模型:采用(2×D×S/H)^0.5经济订货量公式时,需同步计算安全库存=Z×σ×√L,其中服务水平系数Z取值1.65(95%)到2.33(99%)
三、数字化革新实践
1. 预测系统:某汽车零部件商引入LSTM神经网络预测,预测误差从23%降至7%,库存准确率提升至98%
2. 物联网应用:RFID技术使某航空器材商的库存盘点效率提升15倍,实时可视化管理降低呆滞库存27%
3. 区块链溯源:某医疗器械企业通过分布式账本技术,实现配件全生命周期追踪,质保索赔处理效率提升60%
四、行业差异化管理策略
1. 快消行业:实行VMI供应商管理库存,周转率可达25-30次,库存天数控制在12-15天
2. 工业装备:采用备件池共享模式,某风电集团区域库存下降40%,服务响应时间缩短35%
3. 电商平台:通过AI动态定价系统,某3C配件卖家库存周转提升50%,滞销品占比从18%降至6%
五、战略价值延伸
1. 现金流维度:周转率每提升1次,相当于释放10-15%的营运资金
2. 碳足迹影响:某物流企业通过优化周转降低30%库存,年减少仓储能耗相当于1500吨标煤
3. 客户体验:配件可及率提升至99.5%时,客户留存率可提高22个百分点
结语:在数字经济时代,配件周转管理已从成本控制工具进化为战略竞争力载体。企业需构建包含需求感知、智能预测、弹性供应、数字执行的协同体系,在周转效率与供给稳定间找到动态最优解。未来竞争将聚焦于数据驱动的库存神经网络建设,实现从”经验备货”到”认知仓储”的质变升级。
点击右侧按钮,了解更多行业解决方案。
相关推荐
配件周转率计算公式是什么
配件周转率计算公式是什么
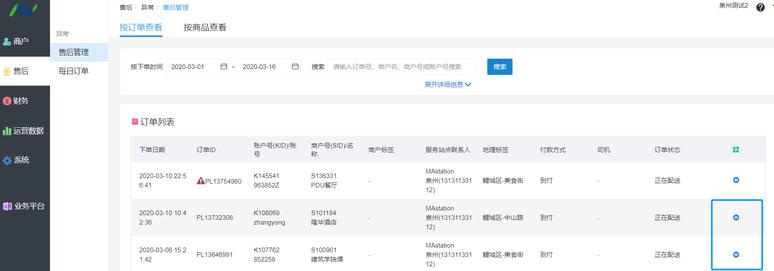
配件周转率是衡量企业库存管理效率的重要指标,反映配件从采购到销售的全周期流转速度。以下为详细解析:
一、核心计算公式
1. 周转次数 = 年度销售成本 / 平均库存成本
- 年度销售成本:全年销售配件的成本总额
- 平均库存成本 =(期初库存 + 期末库存)/2
2. 周转天数 = 365天 / 周转次数
二、计算步骤详解
1. 数据采集阶段:
- 财务年度需统一(自然年或财年)
- 库存成本取值:建议使用移动加权平均法
- 销售成本计算:需扣除退货及折让
2. 计算示例:
某汽配企业年度销售成本480万元,期初库存60万,期末库存100万
平均库存 = (60+100)/2=80万元
周转次数 = 480/80=6次
周转天数 = 365/6≈60.8天
三、指标深度解析
1. 行业对比参考值:
- 汽车行业:4-8次/年
- 电子配件:8-12次/年
- 工业设备:3-5次/年
2. 影响因素矩阵:
- 采购端:供应商交货周期、MOQ(最小起订量)
- 销售端:需求预测准确率、渠道管理能力
- 运营端:仓储物流效率、呆滞库存处理机制
四、优化策略体系
1. 采购优化:
- 实施VMI供应商库存管理
- 建立动态安全库存模型
- 采用经济订购量(EOQ)公式:√(2DS/H)
(D=年需求量,S=单次订货成本,H=单位库存持有成本)
2. 库存结构管理:
- ABC分类法:A类(20%SKU占80%价值)重点监控
- FSN分析法:按流动速度分级(Fast/Slow/Non-moving)
3. 数字化工具应用:
- 部署WMS仓储管理系统
- 应用机器学习进行需求预测
- 建立库存健康度仪表盘
五、常见误区警示
1. 数据口径错误:
- 误用销售收入代替销售成本
- 忽略在途库存计算
- 未扣除已计提坏账的库存
2. 指标误判:
- 单纯追求高周转导致缺货损失
- 忽视不同SKU的特性差异
- 未考虑战略备货的特殊需求
六、延伸分析模型
1. 周转率与毛利率关联分析:
- 构建库存周转率-毛利率矩阵
- 识别高周转高毛利战略品类
2. 现金流影响测算:
- 库存资金占用成本 = 平均库存 × 资金成本率
- 周转率提升10%对ROI的影响模型
七、行业最佳实践
1. 丰田零件中心:
- 实施Milk-Run循环取货
- 周转天数控制在45天以内
- 建立三级库存缓冲体系
2. 华为备件管理:
- 全球协同云仓系统
- 动态仿真补货模型
- 7×24小时紧急调配机制
正确运用周转率指标需要结合企业战略定位,平衡服务水平和库存成本。建议企业每月进行周转率趋势分析,每季度开展库存健康度审计,将周转率指标纳入部门KPI考核体系,同时配合使用库存覆盖天数、呆滞比率等辅助指标,构建完整的库存管理仪表盘。通过持续优化,优秀企业可将配件周转效率提升30%-50%,显著增强市场竞争力。
点击右侧按钮,了解更多行业解决方案。
配件周转率怎么算
配件周转率怎么算
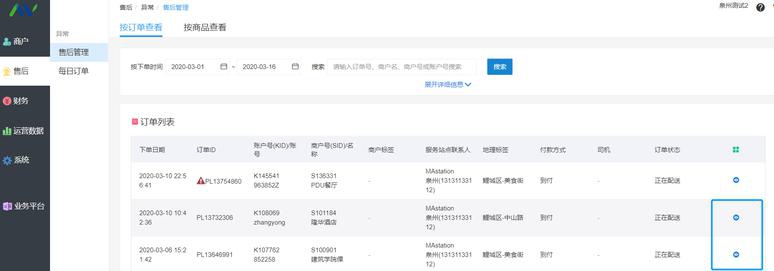
配件周转率计算方法及优化策略
一、配件周转率的定义与意义
配件周转率是衡量企业库存管理效率的核心指标,反映特定周期内配件从采购到销售的流转速度。该指标直接影响企业资金使用效率、仓储成本和市场响应能力。高周转率意味着库存流动性强,资金占用少;低周转率则可能预示滞销风险或采购策略失误。
二、基础计算公式
1. 周转次数公式
[
text{周转率(次)} = frac{text{期间销售成本}}{text{平均库存金额}}
]
示例:某汽配公司年度销售成本240万元,全年平均库存60万元,则周转次数为4次。
2. 周转天数公式
[
text{周转天数} = frac{365}{text{周转次数}}
]
上述案例中,周转天数=365/4≈91天
三、分步计算指南
1. 确定统计周期
根据管理需求选择月/季/年,建议初次计算使用季度数据(平衡季节波动)。
2. 数据采集要点
- 销售成本:包含配件采购价+相关税费(不含人工等运营成本)
- 库存取值:建议使用(期初库存+期末库存)/2,多节点数据可加权平均
3. 特殊场景处理
- 多仓库企业:需合并所有仓库数据
- 混合库存:将非配件类库存剔除后再计算
四、影响要素深度解析
1. 市场需求特性
- 季节性波动(如空调配件夏季需求激增)
- 产品生命周期(新款车型配件周转先快后慢)
2. 供应链效率
- 供应商交货周期:某轴承品牌交货期从45天缩短至30天,周转率提升18%
- 物流时效:区域配送中心建设使周转天数减少7天
3. 库存管理质量
- 安全库存设置:某企业将安全库存从30天用量降至20天,周转率提高22%
- 呆滞库存占比:5%以上的呆滞库存会使整体周转率下降1-2次
五、提升周转率的实操策略
1. 动态采购模型
- 实施滚动需求预测(3个月+1个月修正)
- 经济订单量(EOQ)优化:某企业通过EOQ模型降低采购频次40%,库存减少25%
2. 智能库存分级
- ABC分类法进阶应用:
| 分类 | 金额占比 | 品种占比 | 管理策略 |
||-|-|-|
| A类 | 70% | 10% | 每日监控 |
| B类 | 25% | 30% | 周度核查 |
| C类 | 5% | 60% | 季度盘点 |
3. 供应商协同管理
- 建立VMI(供应商管理库存)体系,某制造企业通过VMI实现周转率提升35%
- 实施JIT准时制配送,将库存周转周期压缩至72小时
4. 数据化监控体系
- 建立周转率仪表盘,关键指标包括:
- 实时库存可视化
- 周转率趋势分析
- 呆滞库存预警(超过180天自动标红)
六、行业基准参考值
不同行业的合理周转率区间差异显著:
- 汽车4S店:年周转4-6次
- 工业设备维修:年周转2-3次
- 电子产品售后:年周转8-12次
七、应用案例解析
某工程机械服务商通过以下措施实现周转率优化:
1. 建立需求预测模型(准确率提升至85%)
2. 实施寄售库存模式(降低自有库存30%)
3. 开发库存共享平台(跨区域调拨效率提升40%)
结果:周转率从2.1次提升至3.8次,年节省资金成本280万元。
八、注意事项
1. 避免单纯追求高周转率导致缺货损失
2. 需结合毛利率分析(高毛利商品可适当放宽周转要求)
3. 定期(季度)进行周转结构分析,识别异常波动
通过系统化应用周转率分析工具,企业可构建更敏捷的供应链体系。建议每月跟踪核心品类周转数据,每季度进行深度分析,持续优化库存结构。实际应用中需结合ERP系统数据,建立自动化的分析模型,提升决策效率。
点击右侧按钮,了解更多行业解决方案。
配件周转率多少合适
配件周转率多少合适
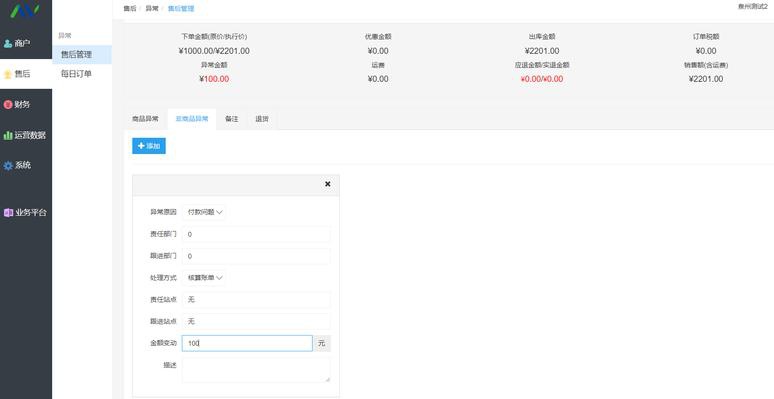
以下是关于配件周转率的详细分析,结构清晰,内容全面:
配件周转率的合理范围及优化策略
一、配件周转率的概念与重要性
配件周转率(Inventory Turnover Ratio)是衡量企业库存管理效率的核心指标,计算公式为:
周转率 = 年度销售成本 / 平均库存金额
该数值反映配件从入库到售出的速度。较高的周转率意味着库存流动性强、资金利用率高,但需避免因过高导致缺货;而过低则可能引发滞销、资金占用等问题。
二、影响合理周转率的四大关键因素
1. 行业特性差异
- 汽车制造业:因配件标准化程度高,周转率通常维持在4-6次/年。
- 医疗设备行业:高价值、长生命周期配件可能仅需2-3次/年。
- 快消电子行业:更新换代快,周转率可达8-12次/年。
2. 供应链稳定性
供应链较长的企业(如依赖进口配件)需维持更高安全库存,周转率可适当降低10%-15%;本地化供应链企业则可追求更高周转效率。
3. 配件属性分类
- 关键件(如发动机部件):需保障供应,周转率建议3-4次。
- 常规件(轮胎、滤芯):可提升至6-8次。
- 长尾件(特殊型号配件):允许1-2次,配合供应商代储策略。
4. 企业战略导向
以成本控制为主的企业可接受较低周转率(如3-4次),侧重现金流的企业则追求6次以上。
三、科学确定合理周转率的四步法
1. 基准对标:参考行业协会数据(如中国汽车流通协会2022年报告显示汽配行业平均周转率为4.7次)。
2. 历史数据分析:对比过去3年周转率趋势,识别季节性波动(如农机配件旺季周转可达淡季的2倍)。
3. ABC分类管理:
- A类(占销售额70%):周转率6-8次
- B类(20%):4-5次
- C类(10%):2-3次
4. 财务模型验证:通过ROI计算,平衡库存成本(约占库存价值20%-30%)与缺货损失。
四、优化周转率的五大实操策略
1. 需求预测升级
- 应用机器学习算法,将预测准确率提升至85%以上
- 建立跨部门S&OP(销售与运营计划)协同机制
2. 供应链协同创新
- 实施VMI(供应商管理库存),将慢流件库存转移至供应商
- 建立区域共享仓,降低各网点安全库存30%
3. 库存结构优化
- 设定动态安全库存公式:
安全库存 = Z值 × √(提前期 × 需求标准差)
- 对180天未动销配件启动强制清理机制
4. 数字化工具应用
- 部署WMS(仓储管理系统)实现实时库存可视
- 应用RFID技术,将盘点效率提升70%
5. 绩效考核体系重构
- 将周转率纳入采购人员KPI,权重不低于30%
- 设立库存健康度指数,包含周转率、库龄、滞销比等维度
五、风险控制与动态调整
建立红黄蓝预警机制:
- 红色(周转率>行业均值150%):启动缺货应急预案
- 黄色(位于均值80%-120%):正常监控
- 蓝色(<80%):触发库存优化项目 每季度进行PDCA循环评估:通过Plan-Do-Check-Act流程持续改进,建议每次调整幅度不超过20%,避免供应链震荡。 六、行业前沿实践 特斯拉采用的"数字孪生"库存系统,通过虚拟仿真将周转率提升40%;京东工业品通过智能补货算法,将MRO配件周转率优化至行业平均水平的2倍。 总结:合理的配件周转率并非固定数值,而是动态平衡的艺术。企业应通过数据驱动决策,结合自身行业特性、供应链能力和战略目标,建立弹性化的库存管理体系。建议每半年全面评估一次周转率标准,在保障服务水准的前提下,逐步向行业标杆靠拢,最终实现库存成本与运营效率的最优解。
点击右侧按钮,了解更多行业解决方案。
免责声明
本文内容通过AI工具智能整合而成,仅供参考,e路人不对内容的真实、准确或完整作任何形式的承诺。如有任何问题或意见,您可以通过联系1224598712@qq.com进行反馈,e路人收到您的反馈后将及时答复和处理。