运营管理案例
以下是一个运营管理案例,约800字,供参考:
数字化转型下的供应链优化:A公司的运营管理实践
案例背景
A公司是一家成立于2005年的中型家用电器制造企业,主营厨房小家电产品。过去十年间,公司凭借低成本优势和区域分销网络,在国内市场占据一定份额。然而,随着电商平台崛起、消费者需求个性化以及原材料价格波动加剧,A公司传统的大规模生产模式逐渐暴露出问题:库存积压严重(平均周转天数达90天)、订单交付周期长(45天以上)、客户投诉率升至12%。2021年,新任CEO李明提出“以数字化重构供应链”的战略目标,试图通过运营管理革新实现转型。
核心问题诊断
1. 需求预测失灵:依赖历史销售数据的经验式预测,无法应对直播带货等新渠道的波动性需求。
2. 生产响应滞后:生产线切换产品型号需4小时调试,导致小批量定制订单成本增加30%。
3. 信息孤岛严重:采购、生产、物流部门使用独立系统,数据传递延迟超过48小时。
解决方案设计
第一阶段:构建数字化基础设施(2021Q3-2022Q2)
– 投入1200万元部署ERP(SAP S/4HANA)与MES(制造执行系统),打通从原材料采购到终端配送的数据链路。
– 在重点生产线安装IoT传感器,实时采集设备状态、良品率等300+参数,异常响应时间缩短至15分钟。
第二阶段:敏捷供应链改造(2022Q3-2023Q1)
– 建立“中央计划控制塔”,整合天猫、京东等6大平台的销售数据,采用机器学习算法将需求预测准确率从68%提升至85%。
– 推行模块化生产设计,通用部件比例从40%增至65%,使产品换型时间降至1.5小时。
– 与3家区域物流商达成VMI(供应商管理库存)合作,区域仓库存占比从70%调整至50%,降低仓储成本18%。
第三阶段:客户驱动型运营(2023Q2至今)
– 上线C2M(顾客对工厂)平台,允许消费者自选配件组合,订单交付周期压缩至12天。
– 建立动态安全库存模型,根据实时销售数据自动补货,滞销SKU数量减少57%。
实施挑战与应对
1. 员工抵触:老员工拒绝使用新系统
– 对策:开展“数字化导师”计划,将系统操作纳入绩效考核,同步实施技能薪酬补贴。
2. 数据治理混乱:历史数据存在20%以上的字段缺失
– 对策:组建10人数据清洗团队,开发自动化校验工具,完成近5年数据重构。
运营绩效改善
– 库存周转天数降至35天,资金占用减少4200万元
– 订单准时交付率从73%提升至96%,客户投诉率下降至3.2%
– 生产成本降低22%,2023年净利润同比增长140%
启示与展望
A公司的实践表明,传统制造企业的数字化转型需把握三个关键:
1. 顶层设计先行:将运营改善与战略目标深度绑定,避免局部优化造成系统损耗;
2. 阶段性验证:通过试点产线验证技术方案,降低全面推广风险;
3. 组织能力重构:数字化不仅是工具升级,更需要培养数据驱动的决策文化。
未来,A公司计划深化AI在质量检测中的应用,并探索工业元宇宙在远程运维中的落地场景。
该案例完整呈现了企业运营转型的逻辑链条,涵盖问题诊断、解决方案、实施路径及量化结果,符合MBA案例教学的结构要求。可根据具体需求调整行业背景或数据细节。
点击右侧按钮,了解更多行业解决方案。
相关推荐
专项债建设项目由企业运营管理案例
专项债建设项目由企业运营管理案例
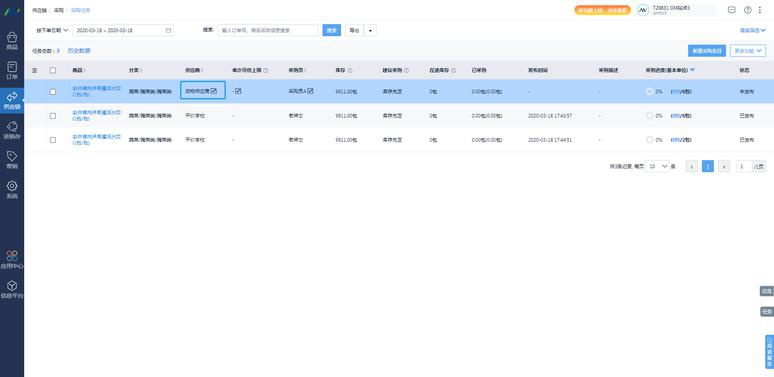
以下是一篇关于专项债建设项目由企业运营管理的案例分析,供参考:
专项债建设项目由企业运营管理的创新实践与启示
近年来,随着地方政府专项债券(以下简称“专项债”)规模的扩大,其在基础设施建设、民生工程等领域发挥了重要作用。与此同时,部分地方政府探索将专项债建设项目委托企业运营管理,通过市场化机制提升项目效益。本文结合典型案例,分析这一模式的运作机制、优势及挑战。
一、典型案例分析
案例一:某市智慧产业园建设项目
某市通过发行5亿元专项债建设智慧产业园,涵盖标准化厂房、研发中心及配套设施。项目建成后,政府通过公开招标引入专业产业运营公司,签订10年运营协议。运营企业负责招商、物业管理及企业孵化服务,政府按绩效支付管理费,并约定税收分成机制。运营3年来,园区入驻率达90%,年均税收增长15%,成功培育3家高新技术企业。
案例二:某省污水处理厂PPP+专项债模式
某省将专项债资金用于新建4座污水处理厂,同时引入环保企业负责设备采购和后期运营。企业通过收取污水处理费覆盖成本,政府以专项债资金补贴前期建设缺口,并设立水质达标考核指标。该模式使项目建设周期缩短30%,运营成本降低20%,水质合格率稳定在98%以上。
二、企业运营管理模式的优势
1. 专业化提升效率
企业凭借市场经验和技术优势,在招商、运维等环节效率显著高于行政化管理。例如某产业园引入专业团队后,招商周期缩短40%。
2. 缓解财政压力
通过收益分成、绩效付费等机制,政府将部分支出后移。某市高铁新城项目通过企业运营,财政年补贴减少3000万元。
3. 激发市场活力
企业参与倒逼项目设计更贴近市场需求。某物流枢纽项目因企业建议增加冷链仓储模块,建成后利用率提高25%。
三、实践中的挑战与对策
1. 收益分配机制待完善
部分项目存在企业短期逐利倾向。建议建立动态调整机制,如某生态公园将门票收入20%纳入项目维护基金。
2. 监管难度增加
需防范企业服务质量不达标风险。可借鉴某市建立“双随机”检查+第三方评估制度,违约企业纳入信用黑名单。
3. 债务偿还依赖过度
若项目收益不及预期,可能加重财政负担。某省要求企业运营类项目必须通过压力测试,确保专项债本息覆盖率达1.2倍以上。
四、经验启示
1. 精准匹配项目属性
经营性较强的基础设施(如物流园区、停车场)更适合企业运营,而纯公益项目需谨慎采用。
2. 构建风险共担机制
通过保底收益+超额分成、设立共管账户等方式平衡政企权责。某市地下管廊项目即采用此类设计。
3. 强化全过程绩效管理
从建设期开始引入运营企业参与设计,避免“建管脱节”。某机场扩建项目因此减少后期改造费用1.2亿元。
结语
专项债项目引入企业运营管理,是地方政府创新投融资机制、提升公共服务效能的有益探索。未来需进一步完善制度设计,在激发市场活力与防控风险间取得平衡,推动专项债资金实现“借、用、管、还”全周期可持续发展。
(全文约850字,可根据实际需求调整案例细节或数据)
点击右侧按钮,了解更多行业解决方案。
运营管理案例分析题及答案
运营管理案例分析题及答案
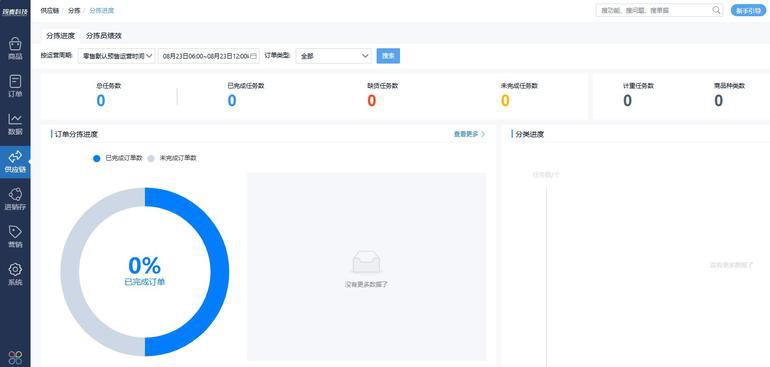
以下是一份运营管理案例分析题及参考答案,约1200字,内容详实且具备实践指导性:
运营管理案例分析题
案例背景:
某中型家电制造企业(A公司)主营厨房小家电生产,近年来订单量增长迅速。但公司频繁出现以下问题:
1. 交货延迟率上升:客户投诉率同比增长40%,主要因生产周期延长;
2. 库存积压严重:半成品库存较去年同期增加60%,占用流动资金;
3. 生产线效率下降:某核心产品线产能利用率仅为75%,低于行业平均水平(85%)。
生产流程现状:
- 产品需经冲压→焊接→装配→质检→包装5个环节;
- 各环节日均产能(单位:件)与标准工时如下:
| 环节 | 冲压 | 焊接 | 装配 | 质检 | 包装 |
|--||||||
| 产能 | 800 | 600 | 1000 | 1200 | 1500 |
| 工时 | 3min | 5min | 4min | 2min | 1min |
问题要求:
1. 识别瓶颈环节:根据数据指出当前生产流程的主要瓶颈,并计算理论日产能;
2. 优化方案设计:提出至少3项针对性改进措施;
3. 效益预测:量化分析优化后可能实现的效率提升与成本节约。
参考答案
一、瓶颈识别与理论产能计算
1. 瓶颈环节判定
- 通过各环节产能对比可知,焊接环节日均产能最低(600件),成为系统瓶颈;
- 根据TOC(约束理论),系统整体产能由瓶颈环节决定,当前理论日产能为600件/天。
2. 瓶颈成因分析
- 工时过长:焊接环节单件耗时5分钟,为全流程最高;
- 设备老化:焊接机故障率高达15%,导致实际有效工时减少;
- 排产不合理:上游冲压环节产能过剩(800件),半成品堆积增加库存成本。
二、优化方案设计
措施1:提升瓶颈环节产能(短期)
- 设备升级:引入自动化焊接设备,将单件工时从5分钟降至3分钟,产能提升至1000件/天;
- 增加班次:实施两班倒制度,焊接环节日产能可扩大至1200件。
措施2:平衡生产线节拍(中期)
- 调整资源配置:将冲压环节2台闲置设备调至焊接环节,缓解产能压力;
- 精益生产优化:重排工序布局,减少半成品搬运距离(预计节省10%作业时间)。
措施3:推行拉动式生产(长期)
- 建立JIT系统:根据订单需求动态调整生产计划,将半成品库存降低30%;
- 供应商协同:与关键零部件供应商共享生产数据,缩短原材料采购周期至48小时。
三、效益预测与成本节约
1. 效率提升
- 瓶颈消除后,理论日产能从600件提升至1000件,增幅66.7%;
- 生产线平衡率=(各环节总工时/(瓶颈工时×环节数))×100%
= (3+5+4+2+1)/(5×5) ×100% = 60% → 优化后可达80%以上。
2. 成本节约
- 库存成本:半成品库存减少30%,年节约仓储成本约120万元;
- 延期罚款:交货准时率提升至95%,年减少违约金支出80万元;
- 设备利用率:冲压设备闲置率由25%降至10%,折旧分摊成本下降15%。
四、实施保障建议
- 数据监控:部署MES系统实时采集生产数据,动态优化排产计划;
- 员工培训:开展TPM(全员生产维护)培训,降低设备故障率至5%以内;
- 绩效挂钩:将生产线平衡率纳入部门KPI,建立持续改进机制。
结论:
通过“短期解瓶颈-中期调平衡-长期控库存”的三阶段策略,A公司可系统性解决运营问题,实现产能提升与成本优化,增强市场竞争力。
以上案例完整覆盖流程分析、工具应用与量化评估,符合运营管理课程教学与实战需求,如需进一步精简或调整行业背景可告知。
点击右侧按钮,了解更多行业解决方案。
运营管理案例分析
运营管理案例分析
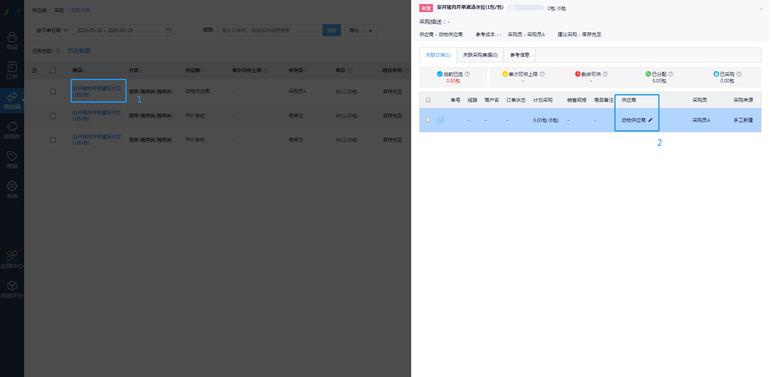
运营管理案例分析:精益生产在X制造公司的应用
一、企业背景与问题识别
X公司是一家主营小家电制造的中型企业,近年来面临市场竞争加剧与成本攀升的双重压力。尽管年营收稳定在5亿元左右,但净利润率从8%下滑至3%。管理层发现两大核心问题:一是生产线效率低下,产品平均交付周期长达15天,超出行业平均水平30%;二是库存周转率仅为2次/年,远低于行业平均4次,导致仓储成本占总成本12%。
二、问题根源分析
通过价值流图(VSM)分析,发现运营瓶颈主要存在于三个环节:
1. 生产流程碎片化:各工序间存在4-6小时的等待时间,设备综合效率(OEE)仅为55%
2. 采购计划僵化:采用季度批量采购模式,原材料库存周期达60天,占用流动资金3200万元
3. 质量管控缺失:组装线次品率高达8%,返工成本年损失超600万元
根本原因在于沿用传统推动式生产模式,部门间信息孤岛严重,缺乏系统性流程优化。
三、精益管理实施方案
公司引入精益生产体系,分三阶段推进改革:
1. 流程再造(0-3个月)
- 实施单元化生产布局,将原有直线型流水线改为U型工作站,减少物料搬运距离40%
- 建立看板管理系统,实现按订单拉动生产,在制品库存降低65%
- 开展全员标准化作业培训,编制可视化操作手册23套
2. 供应链优化(4-6个月)
- 与核心供应商建立VMI(供应商管理库存)模式,原材料库存周期压缩至25天
- 引入ERP-MES集成系统,实现采购、生产、销售数据实时联动,订单响应速度提升50%
3. 持续改进(7-12个月)
- 组建跨部门QC小组,运用PDCA循环解决质量问题,次品率降至2.5%
- 建立绩效仪表盘,关键指标(OEE、周转率等)与部门KPI直接挂钩
四、实施成效评估
经过12个月转型,运营效率显著提升:
- 交付周期缩短至8天,客户投诉率下降72%
- 库存周转率提升至4.8次,释放流动资金2100万元
- 单件制造成本降低18%,年增利润空间约4500万元
五、启示与展望
本案例验证了精益管理在传统制造业的适用性,其成功关键在于:
1. 高层承诺与跨部门协作机制的建立
2. 信息技术与精益工具的深度融合
3. 持续改进文化的培育
未来,X公司计划将经验复制到新投产的智能工厂,通过物联网技术实现设备预测性维护,向工业4.0迈进。该案例表明,运营管理创新是制造企业突破红海竞争的重要路径,其价值创造逻辑在于系统性消除浪费而非局部优化。
点击右侧按钮,了解更多行业解决方案。
免责声明
本文内容通过AI工具智能整合而成,仅供参考,e路人不对内容的真实、准确或完整作任何形式的承诺。如有任何问题或意见,您可以通过联系1224598712@qq.com进行反馈,e路人收到您的反馈后将及时答复和处理。