mes开发
制造执行系统(MES)开发:驱动智能制造的核心引擎
随着工业4.0和智能制造的快速发展,制造执行系统(Manufacturing Execution System, MES)作为连接企业计划层与生产现场的关键纽带,正成为现代制造业数字化转型的核心工具。本文将从MES的定义、核心功能、开发流程及未来趋势等方面,探讨其在工业生产中的价值与应用。
一、MES的定位与核心功能
MES是位于企业资源计划系统(ERP)与车间设备控制系统之间的信息化管理平台,主要负责生产过程的实时监控、调度与优化。其核心功能包括:
1. 生产计划排程:将ERP下达的订单任务转化为可执行的生产指令,并动态调整设备、人员和物料资源。
2. 过程质量控制:通过数据采集分析,实现质量追溯、异常预警和工艺参数优化。
3. 设备管理:监控设备运行状态,预测维护需求,降低非计划停机时间。
4. 物料追溯:建立从原材料到成品的全流程追踪体系,满足合规性要求。
5. 绩效分析:实时生成OEE(设备综合效率)、能耗比等关键指标报表。
二、MES开发的关键流程
1. 需求分析与场景定义
开发初期需深入调研企业生产模式,明确痛点需求。例如离散制造与流程工业对MES的需求差异显著:汽车装配线关注工序协同,而化工厂更侧重批次管理与配方控制。
2. 系统架构设计
采用模块化设计理念,通常包含数据采集层(SCADA/PLC接口)、业务逻辑层(工单管理、质量模块)和可视化层(数字看板)。当前主流技术栈多基于Java/.NET平台,结合微服务架构提升扩展性。
3. 工业物联网集成
通过OPC UA、MQTT等协议连接数控机床、传感器等设备,实现毫秒级数据采集。某电子企业案例显示,集成RFID技术后,物料齐套检查效率提升70%。
4. 算法模型开发
在高级排产(APS)模块中应用遗传算法、深度学习技术,使某光伏企业的设备利用率从65%提升至82%。质量预测模型可提前4小时发现潜在缺陷。
5. 测试与迭代优化
采用数字孪生技术构建虚拟产线,模拟极端工况下的系统稳定性。某项目通过3轮压力测试将系统响应时间从8秒压缩至1.2秒。
三、实施挑战与应对策略
– 数据孤岛问题:通过ESB企业服务总线打通ERP、PLM、WMS等系统,某装备制造商借此实现设计变更到生产执行的闭环周期缩短40%。
– 人员适应性障碍:开发可视化拖拽配置界面,并设计阶梯式培训体系,某食品工厂上线后3周内全员熟练操作系统。
– 安全风险管控:采用工业防火墙+区块链技术,某半导体企业的生产数据泄露事件归零。
四、未来发展趋势
1. 云原生MES:基于容器化部署的SaaS模式降低中小企业应用门槛,某云MES服务商已实现30分钟快速部署。
2. AI深度集成:自然语言处理技术用于工单指令生成,计算机视觉实现自动质检,某案例显示缺陷检出率提升至99.97%。
3. 边缘计算赋能:在车间部署边缘服务器进行实时数据分析,某汽车厂将决策延迟从分钟级降至50毫秒以内。
结语
MES系统的开发不仅是软件工程,更是制造哲学的革新。随着5G、数字孪生等技术的融合,未来的MES将进化成自主决策的“智能生产大脑”,推动制造业从“经验驱动”向“数据驱动”跃迁。对于企业而言,构建与业务深度契合的MES体系,已成为赢得智能制造竞争的战略选择。
点击右侧按钮,了解更多行业解决方案。
相关推荐
mes开发工程师是做什么的
mes开发工程师是做什么的
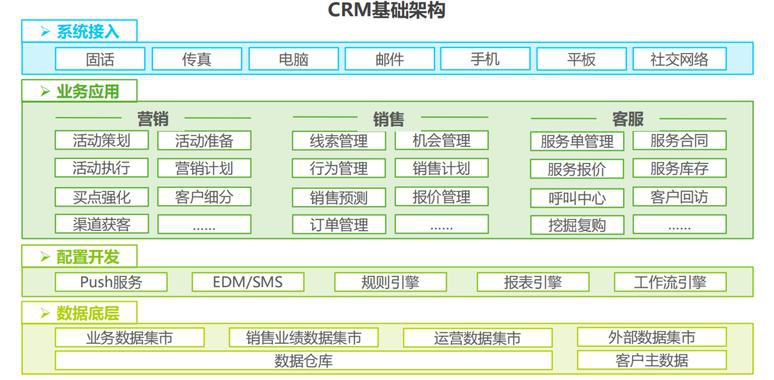
MES开发工程师:制造业数字化的核心推动者
在智能制造和工业4.0的浪潮下,MES开发工程师逐渐成为制造业数字化转型的关键角色。MES(Manufacturing Execution System,制造执行系统)是连接企业计划层(如ERP)与车间设备层(如PLC、传感器)的桥梁,而MES开发工程师则是这一系统的设计者、构建者和优化者。他们的工作直接影响企业生产效率、质量控制与数字化水平。
一、MES开发工程师的核心职责
1. 系统设计与开发
MES开发工程师需根据企业生产需求,设计系统架构并编写核心功能模块。例如:
- 生产调度模块:通过算法优化排产计划,减少设备空闲时间。
- 数据采集模块:对接PLC、SCADA等设备,实时获取产线数据。
- 质量管理模块:设置SPC(统计过程控制)规则,自动触发质量预警。
他们需掌握C、Java等编程语言,并熟悉工业通信协议(如OPC UA、Modbus)。
2. 系统集成与实施
MES需与ERP、WMS(仓储管理系统)、设备层无缝衔接。工程师需解决多系统间的数据孤岛问题,例如:
- 将ERP的生产订单同步至MES,并反馈实际完工情况。
- 整合设备报警信息,实现停机原因自动分析。
这一过程需要熟悉SAP、用友等ERP系统的接口规范。
3. 运维优化与定制化开发
工程师需持续监控系统运行,修复漏洞并响应新需求。例如:
- 为新增产线开发设备接入模块。
- 根据工艺变更调整电子作业指导书功能。
这要求其具备快速理解业务流程和敏捷开发的能力。
二、关键技术能力要求
1. 跨领域知识融合
- 制造业知识:熟悉生产流程(如离散制造的装配线、流程工业的批次管理)。
- IT技术栈:除编程外,需掌握数据库(SQL Server、Oracle)、中间件(Kafka、RabbitMQ)等技术。
- 工业协议:了解Profinet、Ethernet/IP等设备通信协议。
2. 数据分析与算法应用
MES的核心价值在于数据驱动决策。工程师需:
- 利用BI工具(如Power BI)实现OEE(设备综合效率)可视化。
- 应用机器学习预测设备故障(如通过振动数据分析轴承寿命)。
3. 软技能
- 沟通能力:需与生产主管、IT部门及设备供应商协同工作。
- 问题定位能力:快速诊断数据采集异常原因(如网络延迟或协议配置错误)。
三、行业应用场景举例
1. 汽车制造
- 实现整车装配的序列化管理,确保零部件JIT(准时制)配送。
- 通过ANDON系统实时报警,减少生产线停线时间。
2. 电子行业
- 追踪PCB板的生产批次,实现精确的质量追溯。
- 集成AOI(自动光学检测)设备,自动判定产品缺陷。
3. 医药行业
- 符合FDA 21 CFR Part 11电子记录规范,确保数据完整性。
- 管理洁净车间环境参数(温湿度、微粒数),保障GMP合规。
四、职业发展前景
随着智能制造的深化,MES开发工程师的需求持续增长。其职业路径可向技术专家(如工业大数据架构师)、项目经理(主导数字化工厂建设)或产品经理(开发行业化MES解决方案)方向发展。据行业报告,具备5年以上经验的资深工程师年薪可达40-60万元,尤其在新能源、半导体等高附加值产业中更具竞争力。
结语
MES开发工程师不仅是代码编写者,更是制造业效率提升的“隐形推手”。他们通过技术手段将生产数据转化为决策依据,助力企业实现从“经验驱动”到“数据驱动”的跨越。在工业互联网与数字孪生技术兴起的当下,这一角色的重要性将愈发凸显。
点击右侧按钮,了解更多行业解决方案。
mes开发经验是什么
mes开发经验是什么
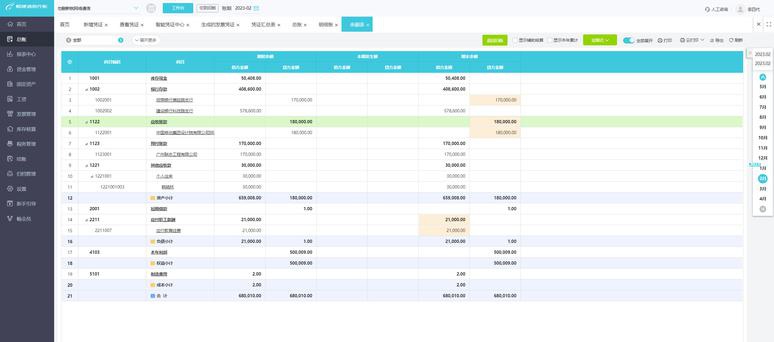
制造执行系统(MES)开发经验是指参与设计、实施和优化MES解决方案的专业能力,其核心在于通过信息技术实现生产过程的精细化管控。随着工业4.0的推进,MES作为连接企业计划层(ERP)与设备控制层(SCADA/PLC)的枢纽,其开发经验已成为智能制造领域的关键竞争力。以下从技术实践、行业理解和综合能力三个维度展开解析。
一、技术实践:全周期开发能力
1. 需求分析与架构设计
MES开发需深入理解离散制造与流程制造的差异,例如汽车行业关注工序节拍,而化工行业侧重批次追踪。通过现场调研提取关键需求,运用UML工具构建包含生产调度、质量管理和设备监控的模块化架构。曾主导某电子厂MES重构项目,通过微服务架构将系统响应速度提升40%。
2. 关键技术栈应用
开发中常采用C/.NET或Java EE技术栈,配合OPC UA实现设备数据采集。数据库设计需兼顾实时性与历史追溯,采用时序数据库InfluxDB处理每秒万级点位数据。在注塑行业项目中,通过Redis缓存机制将看板数据加载时间从8秒降至1.2秒。
3. 系统集成与测试
使用ESB企业服务总线或RESTful API实现与ERP的工单同步,通过MQTT协议对接AGV调度系统。某汽车零部件项目中,开发异常处理中间件,使系统间数据丢包率从0.5%降至0.02%。
二、行业理解:场景化解决方案
1. 合规性适配
医药行业需满足FDA 21 CFR Part 11电子签名规范,开发审计追踪功能时采用区块链存证技术;在半导体领域,构建SPC过程控制模块实现6σ质量管控。
2. 工艺建模能力
为家电装配线开发可视化工艺配置工具,支持拖拽式定义检测工位逻辑,使工艺变更部署周期缩短70%。在食品行业实施批次追溯系统时,采用GS1标准构建从原料到成品的正向/反向追溯链。
3. 数据分析应用
集成机器学习算法实现设备预测性维护,某机床厂案例中,通过振动数据分析将主轴故障预警提前72小时。开发OEE(设备综合效率)分析模块时,引入边缘计算进行实时效能计算。
三、综合能力:价值实现关键
1. 变革管理经验
在实施阶段需应对车间人员数字化抵触,通过开发简化的移动端报工界面,使老工人培训时间从2周缩短至3天。采用渐进式上线策略,先试点关键产线再全面推广。
2. 持续优化机制
建立KPI监控体系跟踪MES使用效果,某项目通过分析系统日志发现质检模块响应延迟,优化数据库索引后单据提交速度提升65%。定期开展用户反馈会,将操作员建议转化为功能迭代。
3. 新技术融合
探索数字孪生技术实现虚拟调试,在新建产线时节省30%试产时间。试验将AR技术应用于设备维修指引,通过MES推送三维拆解动画至工程师智能眼镜。
MES开发不仅是技术工程,更是制造业数字化转型的使能过程。优秀的开发者需兼具软件工程能力与工业基因,在标准化与定制化间取得平衡。随着边缘计算和AI技术的渗透,MES正从执行系统向智能决策系统演进,这对开发者的技术敏锐度和业务洞察力提出了更高要求。持续积累跨行业实践,深入理解精益生产与工业工程原理,将成为MES开发者的核心优势。
点击右侧按钮,了解更多行业解决方案。
mes开发是什么意思
mes开发是什么意思
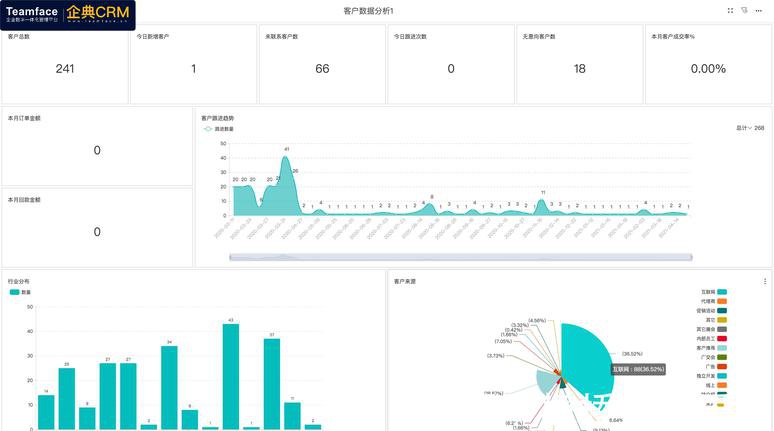
MES开发:定义、流程与制造业数字化转型的核心
一、MES的基本概念
MES(Manufacturing Execution System,制造执行系统)是面向制造业车间层的信息化管理系统,其核心目标是实现生产过程的实时监控、资源优化与效率提升。MES介于企业资源计划系统(ERP)与工业自动化设备之间,充当“桥梁”角色,将计划指令转化为具体生产操作,同时反馈现场数据支持管理决策。
二、MES开发的核心内容
MES开发指围绕制造执行需求,设计、构建并部署定制化系统的全过程,包含以下关键环节:
1. 需求分析与规划:深入调研企业生产流程,明确痛点(如质量追溯困难、设备利用率低),确定系统功能模块(如工单管理、物料追踪)。
2. 系统架构设计:采用分层架构(数据采集层、业务逻辑层、交互层),兼容物联网设备接口,确保可扩展性。
3. 功能模块开发:
- 生产调度:基于订单优先级、设备状态智能排产。
- 质量管理:SPC统计过程控制,实时预警不良品。
- 设备管理:OEE(设备综合效率)分析,预防性维护提醒。
- 数据采集:通过SCADA、RFID等技术实时获取设备与工序数据。
4. 系统集成:与ERP(同步计划与库存)、PLM(集成工艺数据)等系统对接,打破信息孤岛。
5. 测试与部署:模拟真实生产环境进行压力测试,分阶段上线降低风险。
三、MES开发的技术要点
- 工业物联网(IIoT):利用传感器和边缘计算实现设备互联。
- 大数据分析:对生产数据进行挖掘,优化工艺参数。
- 低代码平台:部分场景采用可视化开发,加速功能迭代。
- 云端部署:支持混合云架构,满足灵活性与数据安全需求。
四、行业应用场景示例
- 汽车制造:通过MES实现零部件追溯,精准定位质量问题批次。
- 电子行业:自动化SMT贴片工序监控,减少换线时间。
- 制药企业:符合FDA 21 CFR Part 11规范,确保生产记录不可篡改。
五、MES开发的挑战与趋势
- 挑战:老旧设备数据采集难、跨部门协同阻力、实时性要求高(如毫秒级响应)。
- 趋势:
- AI融合:利用机器学习预测设备故障,动态调整排产。
- 数字孪生:构建虚拟车间仿真,优化生产策略。
- 微服务架构:提升系统模块化,适应柔性制造需求。
六、实施价值
企业通过MES开发可达成:
- 效率提升:减少停机时间20%-30%,缩短订单交付周期。
- 质量改善:降低次品率,实现全流程追溯。
- 成本优化:精准管控物料消耗,减少在制品库存。
结语
MES开发不仅是软件工程,更是对制造业管理逻辑的重构。随着工业4.0推进,MES将向智能化、平台化演进,成为企业打造“透明工厂”、迈向智能制造的核心基石。成功的关键在于紧密结合自身业务,选择适配的技术路径,并持续优化系统与流程的协同。
点击右侧按钮,了解更多行业解决方案。
免责声明
本文内容通过AI工具智能整合而成,仅供参考,e路人不对内容的真实、准确或完整作任何形式的承诺。如有任何问题或意见,您可以通过联系1224598712@qq.com进行反馈,e路人收到您的反馈后将及时答复和处理。