APQP
先期产品质量策划(APQP):构建卓越产品的系统性路径
在全球化竞争日益激烈的制造业中,产品质量已成为企业生存与发展的核心要素。尤其在汽车、航空航天等对安全性和可靠性要求极高的领域,如何在产品开发早期识别潜在风险并制定预防措施,成为企业必须解决的难题。先期产品质量策划(Advanced Product Quality Planning, APQP)作为一种系统化的质量管理方法,通过结构化流程将质量管控前置,帮助企业实现从需求分析到量产交付的全周期质量目标。
一、APQP的核心目标与价值
APQP诞生于美国汽车工业行动集团(AIAG)的标准化实践,其核心在于通过跨部门协作,在产品设计、生产准备阶段提前规划质量管控节点。与传统“事后检验”模式不同,APQP强调预防优于纠正,要求团队在开发初期即识别客户需求(Voice of Customer, VOC),并将其转化为可执行的技术标准。据统计,APQP的规范实施可减少量产阶段60%以上的设计变更成本,同时将产品缺陷率降低30%-50%。
二、APQP实施的五大阶段解析
1. 计划与定义阶段
此阶段需明确产品定位与质量目标,通过QFD(质量功能展开)将客户需求转化为工程特性。例如,某新能源汽车企业通过竞品分析,识别出客户对续航里程的敏感度高于加速性能,从而调整电池管理系统设计优先级。
2. 产品设计与开发
设计团队需同步完成DFMEA(设计失效模式分析),评估潜在设计缺陷。某零部件供应商在开发智能座舱模块时,通过热力学仿真提前发现芯片过热风险,优化散热结构避免后期召回。
3. 过程设计与开发
重点构建制造过程流程图,并开展PFMEA(过程失效模式分析)。某变速箱工厂在工艺设计阶段识别出装配线扭矩检测盲区,增设视觉检测工站后使装配合格率提升至99.8%。
4. 产品与过程验证
通过试生产(试运行)验证制造系统的稳定性,运用SPC(统计过程控制)监控关键参数。某锂电企业在此阶段发现电解液灌注工序的温湿度波动,通过环境控制系统升级将CPK值从1.0提升至1.67。
5. 量产与持续改进
正式投产后建立快速响应机制,结合客户反馈进行PDCA循环优化。某主机厂通过售后数据分析,将APQP经验反哺至新产品开发,使同类故障率每代产品下降约15%。
三、数字化转型下的APQP演进
随着工业4.0技术的普及,APQP正与数字工具深度融合。基于MBSE(基于模型的系统工程)的虚拟样机技术,可在设计阶段模拟产品全生命周期表现;AI驱动的预测性分析能自动识别FMEA中的高风险项;区块链技术则使供应链质量数据可追溯性提升至分钟级。某跨国车企通过部署APQP管理平台,使跨洲协作项目的开发周期缩短40%。
四、实施APQP的关键成功要素
– 跨职能团队建设:质量、研发、生产、采购部门需打破壁垒,建立联合工作小组
– 风险量化管理:引入蒙特卡洛模拟等工具对风险进行概率化评估
– 供应商深度整合:将关键供应商纳入APQP流程,建立联合评审机制
– 知识管理系统:构建APQP案例库,实现经验教训的组织级沉淀
结语
在客户需求日益个性化、产品迭代持续加速的当下,APQP已从汽车行业的专属方法论演变为制造业的通用质量语言。其本质是通过结构化流程将质量管理从被动救火转变为主动防御。当企业真正将APQP思维融入组织DNA,不仅能有效降低质量成本,更能在全球化竞争中构建起难以复制的质量壁垒。未来,随着AI与大数据技术的深度应用,APQP将持续进化,为智能制造时代的产品创新提供更强大的质量基石。
点击右侧按钮,了解更多行业解决方案。
相关推荐
apqp五个阶段
apqp五个阶段
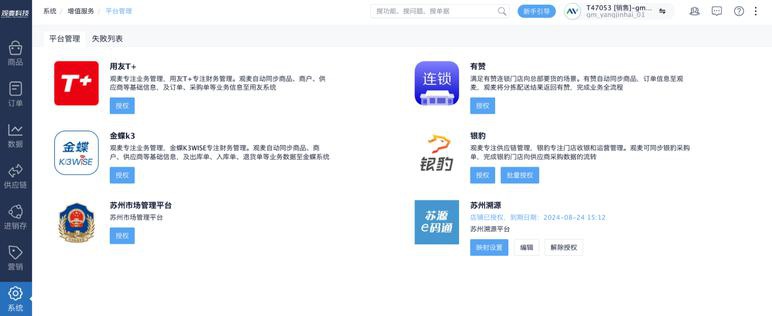
先期产品质量策划(APQP)是汽车行业广泛采用的质量管理框架,旨在通过结构化流程确保产品从设计到量产的全生命周期质量可控。其核心目标是通过预防而非事后检测来减少风险,降低成本并提升客户满意度。APQP包含五个关键阶段,每个阶段环环相扣,形成完整的质量闭环。
一、计划与项目定义
此阶段是APQP的基石,需明确产品定位与质量目标。团队需通过市场调研、竞品分析和客户需求访谈(如VOC分析)确定产品关键特性(CTQ),并制定包含时间节点、资源分配和风险预案的《项目开发计划书》。例如,某新能源汽车项目在此阶段识别出电池续航和安全性能为核心需求,据此设定能量密度≥180Wh/kg的硬性指标。同步启动初步可行性分析,评估技术、供应链及成本限制,确保项目落地性。
二、产品设计与验证
进入工程开发阶段,需将客户需求转化为技术参数。设计部门运用DFMEA工具系统识别潜在失效模式,如某变速箱齿轮组设计时预判热处理变形风险,通过优化齿形参数将风险优先级数(RPN)从192降至64。3D建模后制作快速原型进行功能验证,结合CAE仿真(如热力学分析)优化结构设计。设计评审需跨部门参与,确保可制造性(DFM)和可装配性(DFA),输出完整的工程图纸与技术规范。
三、过程设计与开发
此阶段聚焦制造系统设计,将产品设计转化为可执行的工艺方案。通过PFMEA分析识别生产风险,例如某注塑工艺识别模具排气不良导致气孔的风险,通过增加排气槽和调整保压参数进行控制。需制定详细的《控制计划》,明确关键工序的SPC监控点,如车削工序设定每2小时测量轴径CPK值。同时完成工装夹具设计、设备选型(如选用六轴机器人提升焊接精度)及测量系统分析(MSA),确保量具GR&R≤10%。
四、过程验证与确认
通过试生产(如OTS样件)验证制造系统稳定性。某车企在试制阶段采用25组样件进行全尺寸测量,发现悬架支臂尺寸合格率仅82%,通过优化夹具定位方案提升至99%。完成PPAP文件包提交,包含流程图、FMEA、控制计划等18项要素。过程能力研究要求关键特性CPK≥1.67,如发动机缸体孔径CPK需达1.83。此阶段还需完成操作员培训认证,建立标准化作业指导书(SOP)。
五、持续改进与量产移交
量产初期建立快速响应机制,通过客户装机数据监控早期失效。某零部件企业通过IoT设备实时传输产品运行参数,3个月内将现场故障率从500PPM降至80PPM。定期召开质量评审会,运用8D报告处理异常问题。持续收集产线数据优化过程参数,如通过DOE实验将喷涂良率提升6.5%。最终形成经验教训数据库,为后续项目提供知识储备。
APQP通过这五个阶段的系统推进,将质量管控前移,使质量问题在早期阶段被发现和解决。数据显示,严格执行APQP的企业产品开发周期平均缩短20%,量产问题减少35%。在智能制造的背景下,APQP正向数字化升级,通过PLM系统实现全流程数据贯通,持续推动质量管理的效能提升。
点击右侧按钮,了解更多行业解决方案。
apqp是什么意思
apqp是什么意思
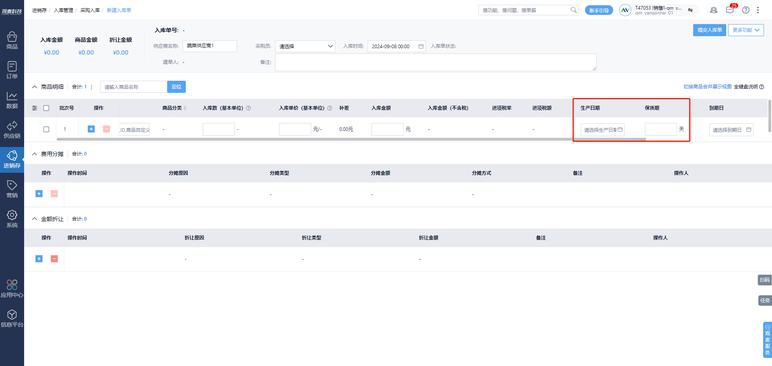
APQP(先期产品质量策划)详解
一、APQP的定义与背景
APQP全称为Advanced Product Quality Planning,中文译为“先期产品质量策划”或“产品质量先期策划”,是汽车行业广泛采用的质量管理工具。它起源于20世纪80年代美国汽车工业行动集团(AIAG)提出的质量管理标准,旨在通过系统化的前期规划,确保产品从设计到量产的全过程满足客户需求,减少质量风险。作为IATF 16949(汽车行业质量管理体系)的核心要求之一,APQP已成为全球汽车供应链中不可或缺的管理方法。
二、APQP的核心目标
APQP的核心在于“预防而非纠正”,强调在产品开发早期识别潜在问题,并制定预防措施。其具体目标包括:
1. 确保客户需求清晰传递:将客户技术要求转化为可执行的设计与生产标准。
2. 降低开发风险:通过跨部门协作,提前发现设计、工艺或供应链中的隐患。
3. 控制成本与周期:减少后期变更和返工,缩短产品上市时间。
4. 提升过程稳定性:建立可重复、可监控的生产流程。
三、APQP的五大阶段
APQP的实施分为五个阶段,每个阶段有明确的输入、输出和活动要求:
1. 计划与确定项目(Plan and Define Program)
- 输入:客户需求、市场分析、历史质量数据。
- 活动:成立跨职能团队,明确项目范围,制定初始质量目标(如缺陷率)、编制项目计划书。
- 输出:设计任务书、初始物料清单(BOM)、风险评估报告(如可行性分析)。
2. 产品设计与开发(Product Design and Development)
- 输入:上一阶段的输出、客户提供的技术规范。
- 活动:完成详细设计(如3D模型、图纸),进行设计失效模式与影响分析(DFMEA),制作原型样件并验证性能。
- 输出:工程样件、设计验证计划(DVP)、更新的BOM。
3. 过程设计与开发(Process Design and Development)
- 输入:产品设计成果、生产设备能力数据。
- 活动:设计生产工艺流程图,制定过程失效模式与影响分析(PFMEA),编制控制计划(Control Plan),确定检验方法与频次。
- 输出:作业指导书(SOP)、测量系统分析(MSA)计划、设备与工装清单。
4. 产品与过程确认(Product and Process Validation)
- 输入:试生产条件(如小批量生产线)。
- 活动:进行试生产(PP,Production Trial),收集数据评估过程能力(如CPK值),完成生产件批准(PPAP),获得客户认可。
- 输出:PPAP提交文件(包括全尺寸报告、材料测试报告)、量产控制计划。
5. 反馈、评估与纠正措施(Feedback, Assessment and Corrective Action)
- 输入:量产后的质量数据、客户投诉信息。
- 活动:持续监控过程稳定性,分析不良品根本原因,实施改进措施(如8D报告)。
- 输出:经验教训库(Lessons Learned)、优化后的控制计划。
四、APQP的关键工具与方法
APQP并非孤立运行,而是与多项质量工具协同使用:
- FMEA(失效模式分析):识别设计与过程中的潜在风险。
- SPC(统计过程控制):通过数据监控生产过程稳定性。
- PPAP(生产件批准程序):确保批量生产符合客户标准。
- QFD(质量功能展开):将客户需求转化为技术参数。
五、APQP的应用范围与行业价值
尽管APQP起源于汽车行业,但其结构化思维已扩展至航空航天、电子制造等领域。例如,某新能源汽车企业在电池开发中应用APQP,通过早期识别热管理风险,将量产后的故障率降低了40%。其核心价值体现在:
- 对企业:减少召回成本,增强供应链协同能力。
- 对客户:获得更高可靠性的产品,缩短交付周期。
六、实施APQP的挑战与对策
1. 跨部门协作难度大:需高层推动建立联合团队,明确职责分工。
2. 资源投入高:可通过数字化工具(如PLM系统)提升文档管理效率。
3. 供应商配合不足:将APQP要求纳入供应商合同,并提供培训支持。
七、总结
APQP的本质是通过系统化策划实现质量前置管理,将“事后检验”转变为“事前预防”。在智能制造与全球化竞争背景下,其价值不仅在于合规性,更是企业构建核心竞争力的关键路径。掌握APQP方法论,能够帮助企业在复杂项目中实现质量、成本与交付周期的平衡,最终赢得客户长期信任。
(全文约850字)
点击右侧按钮,了解更多行业解决方案。
apqp的五个阶段及输出资料
apqp的五个阶段及输出资料
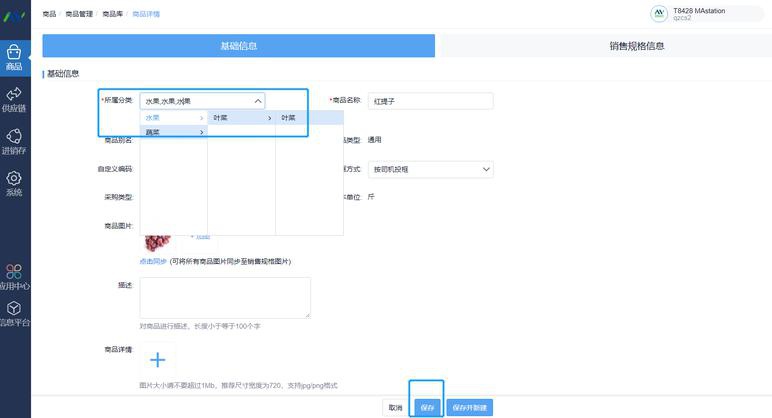
APQP(先期产品质量策划)是汽车行业广泛采用的质量管理工具,旨在通过系统化规划确保产品从设计到量产的全流程质量可控。其核心分为五个阶段,每个阶段均有明确的输出物,确保各环节风险可控。以下详细阐述各阶段要点及关键交付资料:
第一阶段:计划与项目确定
本阶段聚焦客户需求分析与项目可行性评估,为后续开发奠定基础。
核心活动:收集客户技术要求(如SOW)、分析市场定位、评估法律法规、制定初始质量目标。
关键输出:
- 设计目标书:明确产品性能参数(如耐久性指标);
- 初始材料清单(BOM):列出关键零部件规格;
- 可靠性研究计划:定义测试方法(如加速寿命试验方案);
- 项目进度甘特图:细化各节点交付时间及责任人。
例如,某新能源汽车项目在此阶段确定电池续航目标为500公里,并规划了12个月开发周期。
第二阶段:产品设计与开发
将客户需求转化为可执行的设计方案,并通过验证确保设计合理性。
核心活动:完成3D建模、设计失效分析(DFMEA)、样件制作及验证。
关键输出:
- DFMEA报告:识别高风险设计缺陷(如密封结构泄漏风险);
- 工程图纸与CAD数据:标注关键尺寸公差(±0.1mm);
- 设计验证计划(DVP):列明台架试验项目(如振动测试300小时);
- 样件测试报告:记录样件性能数据(如抗拉强度达450MPa)。
某变速箱企业在此阶段通过DFMEA发现齿轮热处理工艺缺陷,提前优化参数避免量产故障。
第三阶段:过程设计与开发
设计可稳定生产的制造流程,确保设计意图转化为实际产能。
核心活动:编制工艺流程图、设计工装夹具、制定过程控制计划。
关键输出:
- 过程流程图(PFD):标注20道关键工序(如焊接、涂装);
- PFMEA文件:评估工序风险(如焊点虚焊RPN值达120);
- 控制计划(CP):定义SPC监控点(如每2小时抽检5件);
- 车间布局图:规划产线节拍(60秒/台)。
某电子企业通过PFMEA发现贴片机精度偏差,增设视觉检测工站后良率提升15%。
第四阶段:产品与过程确认
通过试生产验证制造系统稳定性,确保达到量产标准。
核心活动:进行PPAP提交、MSA分析、产能爬坡验证。
关键输出:
- PPAP文件包:包含尺寸报告、材料认证等18项资料;
- 过程能力报告(CPK≥1.67);
- 试生产总结:记录问题(如注塑缩水率超标)及对策;
- 质量审核清单:覆盖防错装置有效性等50项检查点。
某制动器厂商试生产时发现CPK仅为1.2,通过优化模具温度参数将CPK提升至1.8。
第五阶段:反馈评估与持续改进
量产初期持续监控质量表现,推动持续优化。
核心活动:收集客户投诉数据、实施8D问题解决、更新FMEA。
关键输出:
- 客户满意度报告:跟踪交付准时率(OTD≥98%);
- 售后质量报告(IPTV≤50ppm);
- 经验教训数据库:归档典型问题解决方案;
- 持续改进计划:如导入自动化检测降低人工失误。
某主机厂通过分析首批3个月售后数据,将天窗异响问题改进后索赔率下降70%。
总结
APQP通过结构化流程将质量管控前移,据统计,完整实施APQP的项目量产问题可减少40%以上。各阶段输出物形成完整质量证据链,不仅满足IATF16949体系要求,更有效降低开发成本与市场风险。企业需根据产品复杂度调整文档深度,但核心逻辑始终围绕“预防优于纠正”的质量理念。
点击右侧按钮,了解更多行业解决方案。
免责声明
本文内容通过AI工具智能整合而成,仅供参考,e路人不对内容的真实、准确或完整作任何形式的承诺。如有任何问题或意见,您可以通过联系1224598712@qq.com进行反馈,e路人收到您的反馈后将及时答复和处理。