智能工厂系统
智能工厂系统:驱动制造业数字化转型的核心引擎
在工业4.0浪潮的推动下,智能工厂系统正成为全球制造业转型升级的核心方向。通过整合物联网(IoT)、人工智能(AI)、大数据分析和自动化技术,智能工厂不仅重构了传统生产模式,更在效率、灵活性和可持续性上实现了质的飞跃。本文将深入探讨智能工厂系统的技术架构、应用场景及其对产业未来的深远影响。
一、智能工厂系统的技术基石
智能工厂的构建依赖四大关键技术:
1. 物联网(IoT):通过传感器和工业互联网,实现设备、产品与系统的实时互联。例如,数控机床的运行状态、仓库库存数据等均可被实时采集并上传至云端,为决策提供即时依据。
2. 大数据与AI分析:海量生产数据经机器学习算法处理,可预测设备故障、优化工艺流程。德国西门子安贝格工厂通过数据分析,将产品缺陷率降低了50%。
3. 自动化与机器人技术:协作机器人(Cobots)与AGV无人车协同作业,柔性生产线能快速切换产品型号,满足个性化定制需求。
4. 数字孪生(Digital Twin):虚拟模型同步映射物理工厂,支持从产品设计到运维的全生命周期模拟,缩短研发周期30%以上。
二、应用场景与价值创造
智能工厂的应用已渗透到制造全流程:
– 智能排产:AI算法综合订单、设备状态和供应链数据,动态调整生产计划,某汽车厂商借此将交付周期从14天压缩至5天。
– 预测性维护:振动传感器结合AI模型提前14天预警设备异常,避免非计划停机,某石化企业年维护成本降低25%。
– 质量管控:机器视觉系统以0.01mm精度检测零件缺陷,良品率提升至99.98%。
– 绿色制造:能源管理系统实时优化能耗,施耐德电气武汉工厂通过智能调控年减碳12%。
三、挑战与未来演进
尽管前景广阔,智能工厂落地仍面临多重挑战:
1. 数据安全风险:工业互联网的开放性使黑客攻击威胁倍增,需构建多层防护体系。
2. 技术与人才壁垒:传统企业缺乏AI算法开发能力,复合型人才缺口达76%(工信部2023年数据)。
3. 投资回报周期:初期智能化改造成本高昂,中小企业常面临资金压力。
未来趋势呈现三大方向:
– 云边协同:边缘计算设备实现本地实时决策,与云端深度分析形成互补。
– 人机共融:AR眼镜辅助工人操作,人类专注创造性工作,机器处理重复劳动。
– 产业链协同:通过工业互联网平台,上下游企业共享数据,构建弹性供应链。
结语
智能工厂不仅是技术的堆砌,更是制造思维的革命。它打破了传统工厂的物理边界,推动制造业向网络化、服务化转型。据麦肯锡预测,到2030年智能工厂将释放1.5万亿美元经济价值。在这场变革中,企业需以数据为纽带,持续优化技术生态,方能在全球智造竞争中占据先机。
点击右侧按钮,了解更多行业解决方案。
相关推荐
智能工厂系统架构
智能工厂系统架构
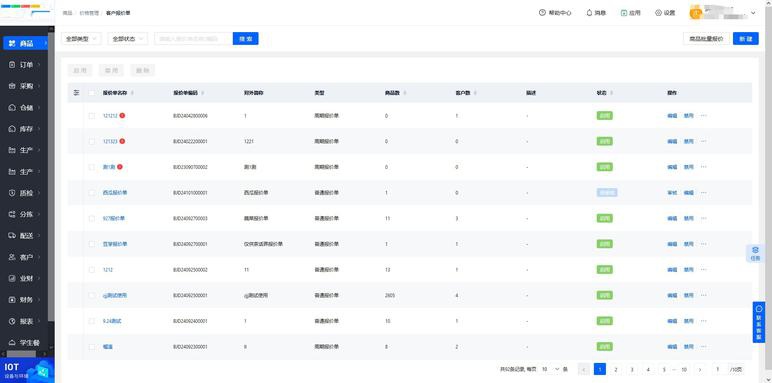
智能工厂系统架构解析:从底层设备到顶层应用的数字化集成
随着工业4.0的深入推进,智能工厂作为制造业数字化转型的核心载体,其系统架构的设计直接决定了生产效率、资源利用率与业务灵活性。本文将从分层架构的角度,解析智能工厂的系统组成及其关键技术。
一、智能工厂架构的分层模型
典型的智能工厂系统架构可分为五层:设备层、网络层、数据层、平台层、应用层,形成自下而上的数据流动与决策闭环。
1. 设备层(感知与控制层)
作为物理世界的入口,设备层由智能传感器、工业机器人、数控机床、AGV(自动导引车)等硬件构成。通过嵌入式系统与边缘计算模块,设备可实时采集振动、温度、压力等工艺参数,并执行控制指令。例如,配备视觉系统的机械臂能自主识别零件位置,实现高精度装配。
2. 网络层(通信与安全层)
该层通过工业以太网、5G、TSN(时间敏感网络)等技术连接设备,构建低时延、高可靠的通信网络。关键要求包括:
- 协议兼容性:支持OPC UA、MQTT等跨平台协议;
- 网络安全:采用零信任架构,通过防火墙、数据加密防范APT攻击;
- 边缘计算节点:在靠近设备端进行数据预处理,减少云端负载。
3. 数据层(存储与治理层)
数据湖或数据仓库在此层汇聚来自设备、ERP、供应链的多源异构数据,需解决以下问题:
- 时序数据库:针对设备高频数据采用InfluxDB、TDengine等专用存储;
- 数据清洗:通过规则引擎过滤异常值,标准化数据格式;
- 元数据管理:建立数据血缘图谱,确保可追溯性。
4. 平台层(分析与服务层)
基于PaaS(平台即服务)构建工业互联网平台,核心功能包括:
- 数字孪生:通过3D建模与仿真技术映射物理产线;
- AI模型训练:利用PyTorch、TensorFlow开发预测性维护算法;
- 微服务编排:通过Kubernetes实现资源弹性调度。
5. 应用层(业务决策层)
面向具体场景开发智能化应用,典型模块如:
- MES(制造执行系统):动态排产与工艺优化;
- QMS(质量管理系统):基于SPC的缺陷根因分析;
- EMS(能源管理系统):实时监控能耗并生成节能方案。
二、关键技术支撑
1. 工业物联网(IIoT)
设备互联与状态监控的基础,全球30%的工厂已部署IIoT平台,设备联网率提升至60%以上。
2. 大数据分析
采用Spark、Flink等流批一体计算框架,实现从设备异常检测(如FMEA分析)到市场预测的全链路洞察。
3. 数字主线(Digital Thread)
贯穿产品全生命周期的数据流,支持从研发设计到售后服务的跨部门协同,某汽车工厂通过该技术将新品交付周期缩短40%。
三、实施路径与挑战
1. 分阶段升级路径
优先改造关键产线,逐步扩展至全厂。例如,某电子制造商首年部署10条智能产线,次年实现SCADA系统全覆盖,三年内完成数字孪生建模。
2. 核心挑战
- 数据孤岛:需打通OT与IT系统接口;
- 人才缺口:复合型工程师培养周期长达3-5年;
- 投资回报率:智能工厂建设成本约是传统工厂的1.8倍,需通过精益管理提升ROI。
四、未来趋势
1. 云边端协同:5G+边缘计算将时延压缩至10ms以内;
2. 自主决策:强化学习算法使设备具备自优化能力;
3. 可持续制造:碳排放数据纳入智能调度模型。
智能工厂系统架构的本质是通过数据驱动实现制造系统的“感知-分析-决策-执行”闭环。随着AIoT、数字孪生等技术的成熟,未来工厂将逐步向“自适应制造”演进,最终达成零缺陷、零停机、零库存的智能制造愿景。
点击右侧按钮,了解更多行业解决方案。
智能工厂系统功能设计
智能工厂系统功能设计
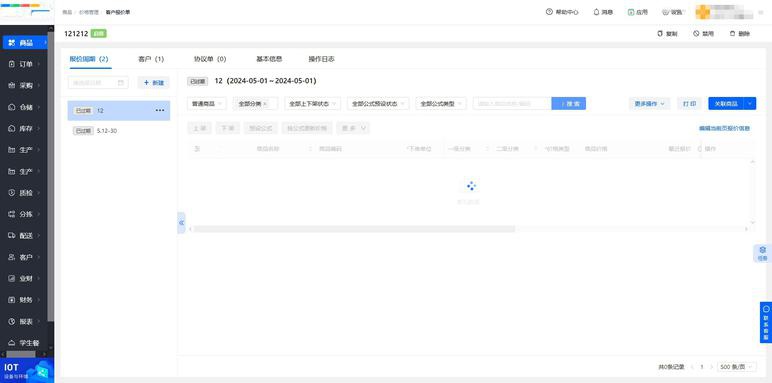
智能工厂系统功能设计(800字)
一、系统架构设计
智能工厂系统采用"云-边-端"三级架构,支持工业4.0标准体系。云端部署ERP、MES、SCADA等核心系统,边缘计算节点实现本地化数据处理,终端设备层包含智能传感器、工业机器人、AGV等物联网设备。系统通过OPC UA协议实现跨平台数据交互,采用5G+TSN网络确保时延<10ms。 二、核心功能模块 1. 智能生产管理 (1)数字孪生建模:构建三维可视化工厂模型,支持设备状态实时映射与工艺仿真 (2)自适应排产系统:集成遗传算法优化排程,动态响应订单变化与设备异常 (3)AGV协同调度:基于实时定位系统(RTLS)实现多车路径规划,运输效率提升40% 2. 设备物联管理 (1)预测性维护:采集200+设备参数,通过LSTM神经网络预测故障,准确率达92% (2)能源优化系统:部署智能电表与热成像仪,建立能耗数字画像,节能15-20% (3)设备OEE分析:实时计算设备综合效率,自动生成改进建议报告 3. 质量管控体系 (1)AI视觉检测:部署深度学习算法,实现微米级缺陷识别,检测速度达1200件/分钟 (2)SPC质量分析:自动生成X-R控制图,异常波动自动触发报警机制 (3)质量追溯系统:应用区块链技术存储生产数据,实现全生命周期追溯 4. 供应链协同 (1)智能仓储管理:采用SLAM导航机器人,库存周转率提升30% (2)供应商看板系统:建立EDI数据交换平台,提前预警物料短缺风险 (3)需求预测模块:融合市场数据与历史销售,预测准确率提升至85% 三、关键技术支撑 1. 工业大数据平台:部署Hadoop集群,日处理数据量达10TB,支持时序数据库存储 2. 边缘AI推理:采用NVIDIA Jetson模组,实现本地化模型推理响应时间<50ms 3. 数字主线(Digital Thread):建立产品全流程数据流,贯通设计-生产-服务环节 四、系统实施效益 1. 生产效率提升:整体设备效率(OEE)从65%提升至85% 2. 质量成本降低:产品不良率从3%下降至0.5%以下 3. 交付周期缩短:订单交付周期压缩40%,准时交付率达99% 4. 人力成本优化:减少30%现场操作人员,技术人才占比提升至45% 五、安全防护体系 1. 建立三级等保架构,部署工业防火墙隔离OT/IT网络 2. 采用国密算法加密关键数据,设置双重身份认证 3. 建立网络态势感知平台,实时监测200+安全威胁指标 该系统通过深度集成新一代信息技术,构建了柔性化、数字化、智能化的现代制造体系,为企业数字化转型提供全面技术支撑。实际应用表明,系统投资回报周期可缩短至18-24个月,助力制造企业实现产能提升与质量飞跃。
点击右侧按钮,了解更多行业解决方案。
智能工厂系统MES,WMS,WCS交换层级关系
智能工厂系统MES,WMS,WCS交换层级关系
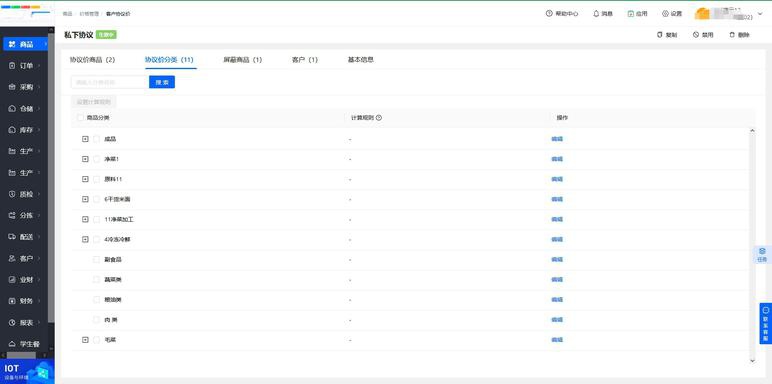
智能工厂作为工业4.0的核心载体,其高效运转依赖于制造执行系统(MES)、仓库管理系统(WMS)和仓库控制系统(WCS)的深度协同。这三个系统通过层级化的数据交互与指令传递,构建起从生产计划到物理执行的全链路闭环。以下从功能定位、层级架构、交互逻辑及技术实现四个维度解析其关系。
一、功能定位:垂直领域的专业化分工
MES 作为制造中枢,聚焦生产现场管理,负责工序调度、质量追溯、设备状态监控及生产数据分析。其核心价值在于将ERP的生产计划转化为可执行的工单,并实时反馈执行结果。
WMS 定位于仓储物流优化,管理物料入库、存储、拣选、出库全生命周期,通过库位优化策略和库存可视化为生产线精准供料。
WCS 作为设备控制层的中枢,直接驱动自动化立体仓库、AGV、输送线等硬件设备,将WMS的仓储策略转化为机械动作指令,确保物理空间与信息空间的精准映射。
二、层级架构:金字塔式控制体系
在智能工厂五层架构模型中,MES处于L3生产运营层,WMS属于L4仓储规划层,而WCS位于L2设备控制层。这种层级关系形成"决策-规划-执行"的金字塔结构:
- MES 接收ERP的月/周级计划后,分解为小时级工单并下发至WMS请求物料配送
- WMS 根据工单需求生成库内作业任务(如拆垛、拣选),通过任务队列传递给WCS
- WCS 将作业指令解析为PLC可执行的设备控制代码,并实时监控设备状态反馈至上层系统
典型数据流表现为:MES工单→WMS作业指令→WCS设备信号→传感器数据反向传递的闭环。
三、交互逻辑:事件驱动的动态协同
三系统通过SOA(面向服务架构)实现松耦合集成,关键交互节点包括:
1. 生产触发备料:MES启动工单时,向WMS发送物料需求清单(BOM),触发备料流程
2. 动态库存调整:WMS实时更新库位状态至MES,支持生产排程的动态优化
3. 异常处理联动:当WCS检测到设备故障时,逐级向上传递告警,触发WMS调整出库策略、MES重排生产计划
4. 数据孪生同步:WCS采集的设备运行数据(OEE、MTBF)上传至MES,支撑产能分析决策
例如在汽车焊装车间,MES下发白车身生产指令后,WMS自动匹配所需钢板库存,WCS调度堆垛机取料并通过AGV配送至生产线边库,全过程时延需控制在5分钟内。
四、技术实现:工业物联网架构支撑
为实现毫秒级响应,系统间采用混合通信协议:
- MES-WMS 间通过RESTful API交换结构化数据(JSON/XML格式)
- WMS-WCS 采用OPC UA实现实时数据流传输,保障设备控制指令的低时延
- 边缘计算节点 处理WCS与PLC的PROFINET/EtherCAT通信,降低云端负载
数据中台作为信息枢纽,通过Kafka消息队列实现三系统数据流的削峰填谷,利用时序数据库存储设备运行日志,为数字孪生提供数据支撑。
五、演进趋势:AI驱动的自主协同
随着工业AI发展,三系统边界逐渐模糊:
- MES集成预测性维护算法,提前触发WMS备件调拨
- WMS应用强化学习优化库位分配,降低WCS设备空驶率
- WCS结合计算机视觉实现异常工况自主决策
这种智能化演进正在重构传统层级关系,形成以生产目标为导向的自主协同网络。某光伏企业通过三系统深度集成,实现库存周转率提升40%,生产换型时间缩短65%,印证了系统间有机协同的价值。
结语:MES-WMS-WCS的层级协作本质是"决策-资源-执行"的价值传递链。随着工业互联网平台的普及,三系统正从单向指令传递向双向智能交互演进,推动制造系统从自动化向自主化跨越。未来竞争力将取决于系统间数据流动的效率与智能决策的精准度。
点击右侧按钮,了解更多行业解决方案。
免责声明
本文内容通过AI工具智能整合而成,仅供参考,e路人不对内容的真实、准确或完整作任何形式的承诺。如有任何问题或意见,您可以通过联系1224598712@qq.com进行反馈,e路人收到您的反馈后将及时答复和处理。